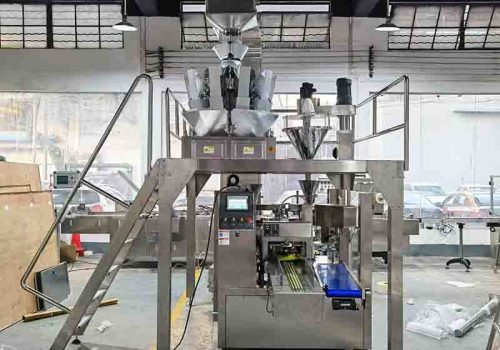
Vertical Form Fill Seal Machine
Column 1 | Column 2 |
---|---|
Row 1, Col 1 | Row 1, Col 2 |
Row 2, Col 1 | Row 2, Col 2 |
Row 3, Col 1 | Row 3, Col 2 |
Row 4, Col 1 | Row 4, Col 2 |
Row 5, Col 1 | Row 5, Col 2 |
A very effective and adaptable automated packaging device, the Vertical Form Fill Seal Machine (VFFS) is used extensively in the food, pharmaceutical, and chemical sectors. This machine is ideal for packaging dry granules or tiny items like chocolates, peanuts, pistachios, melon seeds, green beans, jelly, rice grains, little biscuits, coffee beans, and more since it can automatically create, fill, seal, and cut bags.
- Packaging Speed: Depending on the bag length and product specifications, the Vertical Form Fill Seal Machine can package 5 to 55 bags per minute. It is the perfect option for large-scale manufacturing lines because of its high-speed capabilities.
- Packaging Range: With a maximum film width of 720mm, the machine can handle bags with lengths between 100 and 500mm and widths between 180 and 350mm. It can accept a variety of product sizes and shapes because to its flexible packaging range.
The Vertical Form Fill Seal Machine guarantees sanitary, secure, and reliable product packaging with its fast packing speed, accurate measurement, and movable features. The Vertical Form Fill Seal Machine offers dependable packaging solutions for both small-batch and large-scale manufacturing, assisting companies in improving product quality and production efficiency.
Filling Machine Guide
How to Choose the Best Filling Machine Why Choose Weighing Filling for Coffee and Milk Powder Applications of Vertical Form Fill Seal Machine What Problems Does the VFFS Machine Solve? Conclusions1. Gravity Filling
- ✓ Simple & Cost-Effective - Uses natural gravity flow, requiring minimal mechanical components, reducing initial and maintenance costs.
- ✓ Gentle on Products - Ideal for fragile or shear-sensitive liquids (e.g., wine, oils) as it avoids high-pressure pumping.
- ✓ Low Energy Consumption - No need for pumps or compressors, making it energy-efficient.
- ✓ Easy to Clean & Maintain - Fewer moving parts simplify sanitation, making it suitable for food and beverage industries.
- ✓ Suitable for Low-Viscosity Liquids - Works well with thin, free-flowing liquids like water, juice, and alcohol.
- ✗ Limited to Low-Viscosity Liquids - Not suitable for thick or viscous products (e.g., honey, syrups).
- ✗ Slower Filling Speed - Relies on natural flow, making it less efficient than pressure or vacuum filling for high-speed production.
- ✗ Less Precise for Foamy Liquids - Carbonated beverages or foamy liquids may cause inconsistent fill levels.
- ✗ Requires Consistent Liquid Level - The filling tank must remain at a stable height to maintain accuracy.
- ✗ Not Ideal for Aseptic Packaging - Open design increases contamination risk for sterile products.
2. Pressure Filling
- ✓ Handles High-Viscosity Liquids - Ideal for thick products like sauces, pastes, and syrups that don't flow easily under gravity.
- ✓ Faster Than Gravity Filling - Uses external pressure (pneumatic or mechanical) to speed up the filling process.
- ✓ Precise & Consistent - Better control over fill volume, reducing overfills or underfills.
- ✓ Works with Foamy Liquids - Minimizes foam formation compared to gravity filling, making it suitable for shampoos, detergents, and some beverages.
- ✓ Flexible for Different Container Shapes - Can fill bottles, pouches, or irregularly shaped containers effectively.
- ✗ Higher Equipment Cost - Requires pumps, compressors, or pressurized systems, increasing initial investment.
- ✗ More Maintenance Needed - Seals, valves, and pumps need regular upkeep to prevent leaks or pressure loss.
- ✗ Not Ideal for Fragile Products - High pressure can damage delicate liquids (e.g., some dairy or cosmetic emulsions).
- ✗ Potential for Overpressurization - If not controlled well, excessive pressure can cause spills or container damage.
- ✗ Limited for Carbonated Drinks - Not as effective as isobaric (counter-pressure) filling for retaining carbonation in sodas or beers.
3. Vacuum Filling
- ✓ Prevents Oxidation & Contamination - Ideal for sensitive liquids (e.g., wine, oils, chemicals) by minimizing air exposure.
- ✓ Handles Thin to Medium Viscosity Well - Efficient for water-like or slightly thick fluids (e.g., juices, solvents).
- ✓ Reduces Foaming - Gentle suction avoids agitation, making it suitable for foamy or carbonated liquids.
- ✓ Accurate for Small Bottles - Works well with narrow-neck containers where gravity filling struggles.
- ✓ No Dripping or Spillage - Vacuum suction stops flow precisely, reducing waste and mess.
- ✗ Not for High-Viscosity Liquids - Struggles with thick products (e.g., honey, pastes) that resist suction.
- ✗ Slower Than Pressure Filling - Vacuum generation takes time, limiting high-speed production.
- ✗ Higher Equipment Cost - Requires vacuum pumps and airtight systems, increasing upfront investment.
- ✗ Maintenance Intensive - Seals and valves must stay airtight; leaks disrupt performance.
- ✗ Limited Container Compatibility - Works best with rigid containers (glass, hard plastic); flexible pouches may collapse.
4. Isobaric Filling
- ✓ Perfect for Carbonated Beverages - Maintains carbonation by equalizing pressure between the tank and container (e.g., beer, soda, sparkling water).
- ✓ Minimizes Foam & Oxidation - Prevents CO₂ loss and product degradation, preserving flavor and quality.
- ✓ High Speed & Efficiency - Suitable for high-volume production lines (e.g., breweries, soft drink bottling).
- ✓ Accurate Fill Levels - Pressure control ensures consistent volumes, reducing overfilling or underfilling.
- ✓ Versatile Container Compatibility - Works with glass bottles, cans, and PET containers.
- ✗ High Initial Cost - Complex machinery (pressure regulators, CO₂ systems) increases capital investment.
- ✗ Limited to Carbonated Liquids - Not cost-effective for non-carbonated products (e.g., water, juices).
- ✗ Maintenance Demands - Requires regular calibration of pressure systems to prevent leaks or gas loss.
- ✗ Not for Viscous Products - Designed for low-viscosity liquids; thick fluids (e.g., syrups) may clog valves.
- ✗ CO₂ Dependency - Requires a steady supply of CO₂ or nitrogen, adding operational costs.
5. Volumetric Filling
- ✓ High Precision - Uses fixed-volume chambers (pistons, cups, or augers) for extremely accurate fills, ideal for pharmaceuticals or expensive ingredients.
- ✓ Handles Diverse Viscosities - Works with thin liquids (water) to thick pastes (toothpaste, sauces) by adjusting the mechanism.
- ✓ No Weight Dependency - Unlike weigh-filling, it isn't affected by product density variations.
- ✓ Fast & Repeatable - Suitable for high-speed production with consistent cycle times.
- ✓ Low Product Waste - Minimal residual left in filling nozzles, reducing material loss.
- ✗ Less Flexible for Density Changes - If product density varies (e.g., aerated creams), fill weight may drift despite volume accuracy.
- ✗ Higher Maintenance - Pistons, seals, and augers require regular cleaning and wear-part replacement.
- ✗ Initial Cost - More expensive than gravity filling due to precision components.
- ✗ Not Ideal for Foamy Liquids - Air bubbles can disrupt volume measurement accuracy.
- ✗ Limited for Large Volumes - Typically used for small-to-medium fills (e.g., cosmetics, pharmaceuticals).
6. Weighing Filling
- ✓ Ultra-High Precision - Uses load cells for direct weight measurement, achieving ±0.1% accuracy (ideal for expensive/regulated products like coffee,奶粉,pharmaceuticals).
- ✓ Unaffected by Density Changes - Compensates for variations in particle size,aeration,or viscosity (e.g.,ground coffee vs. whole beans).
- ✓ Zero Product Waste - No residual in nozzles/tubes (critical for high-value materials like spices or APIs).
- ✓ Flexible Packaging - Handles powders,granules,liquids,and even irregular solids (e.g.,nuts,frozen fruits).
- ✓ Compliance Ready - Meets strict FDA/ISO standards for net content verification.
- ✗ Higher Initial Cost - Advanced sensors/controllers make it 2-3× pricier than volumetric/pressure systems.
- ✗ Slower Cycle Times - Weighing process adds 10-30% slower speeds vs. volumetric/pressure filling.
- ✗ Vibration Sensitivity - Requires anti-vibration setups in noisy production environments.
- ✗ Maintenance Complexity - Load cells need frequent calibration; not ideal for corrosive/dusty products.
- ✗ Overfill Risk - Free-flowing products (e.g.,rice) may require dual-stage filling (fast+slow) for accuracy.
7. Time-Pressure Filling
- ✓ High Speed & Efficiency - Uses timed bursts of air pressure for rapid fills (ideal for high-volume liquids like water, oils).
- ✓ Gentle on Products - Low shear stress protects delicate fluids (e.g., emulsions, dairy, cosmetic serums).
- ✓ No Moving Parts in Contact - Reduces contamination risk for sterile/cleanroom applications (pharmaceuticals).
- ✓ Adjustable Precision - Fill accuracy improves with viscosity consistency (e.g., shampoos, sauces).
- ✓ Lower Cost than Weighing - Simpler than load-cell systems but more precise than gravity filling.
- ✗ Viscosity-Dependent - Performance drops with thick or non-Newtonian fluids (e.g., ketchup, honey).
- ✗ Requires Stable Pressure - Compressed air fluctuations cause fill inconsistencies.
- ✗ Not for Foamy Liquids - Pressure can aerate products (e.g., beer, liquid soaps).
- ✗ Limited to Medium Accuracy - Typically ±1-2% error vs. weighing (±0.1%) or volumetric (±0.5%).
- ✗ Maintenance Needs - Nozzles and pressure regulators require frequent cleaning.
8. Peristaltic Pump Filling
- ✓ Ultra-Hygienic & Contamination-Free - Fluid only contacts the tubing, ideal for sterile pharmaceuticals, biotech, and food-grade products (e.g., vaccines, baby food).
- ✓ Handles Shear-Sensitive Fluids - Gentle pumping preserves fragile cells, emulsions, and high-viscosity fluids (e.g., yogurt, cosmetic creams).
- ✓ Precise & Repeatable - Adjustable rollers control flow rates with ±0.5-1% accuracy (suitable for lab-scale to industrial fills).
- ✓ Self-Priming & Dry-Run Safe - No seals/valves to leak; runs dry without damage.
- ✓ Easy Maintenance - Only tubing needs replacement (no complex disassembly).
- ✗ Tubing Wear & Replacement Cost - Frequent use degrades tubing (silicone, PharMed®), increasing long-term costs.
- ✗ Slower Than Piston Pumps - Roller speed limits maximum flow rates (not for high-speed beverage lines).
- ✗ Pulsation Effect - May cause minor filling inconsistencies unless dampeners are used.
- ✗ Limited to Low/Medium Viscosity - Struggles with extremely thick pastes (e.g., peanut butter).
- ✗ Higher Energy Use - Continuous motor operation consumes more power than diaphragm pumps.
For packing goods like milk powder and coffee, weighing filling is a common and effective technique. It is favored over alternative filling techniques for a number of reasons:
1. Accuracy and Precision
The purpose of weighing filling machines is to provide precise and reliable product measures. For goods with delicate, changeable textures, such as milk powder and coffee, it is essential to maintain a constant weight in every box for both quality assurance and consumer pleasure. To ensure uniformity across all packages, the machine weighs the goods precisely and fills each bag using scales.
2. Higher-quality products
Weighing filling devices lower the possibility of overfilling or underfilling, which might result in wasted goods or unhappy customers. Accurate weighing is crucial for powdered goods, such as milk or coffee powder, to prevent air pockets, spills, and clumping in the packaging. This process guarantees that the final packed product is consistent and that the product's integrity is preserved.
3. Economic Efficiency
Weighing filling systems reduce product loss for producers by using accurate measurements. Because fewer personnel are required to guarantee the correctness of the filling process, they also save labor expenses. This guarantees efficiency and lower operating costs, making it the perfect choice for high-volume production settings.
4. Adaptability
Because of its great adaptability, weighing filling systems may be used with a variety of granular and powdered goods, such as coffee, milk powder, tea, spices, and other items of a similar kind. They are flexible enough to meet a range of packaging requirements since they are simple to modify for different bag sizes and product kinds.
5. Automated Procedure
The speed and effectiveness of the packing process are increased by the frequent integration of weighing filling machines into fully automated production lines. Automation lowers the possibility of human mistake and increases productivity by enabling greater throughput with less human interaction.
6. Safety and Hygiene
High standards of cleanliness are essential for goods like coffee and milk powder. Weighing filling systems are often made of materials that avoid contamination and are designed to be easily cleaned. While following stringent industry rules, they aid in ensuring the safe packaging of food goods.
1. Food Industry
- Dry Snacks and Cereals: VFFS machines are perfect for packaging dry food products such as cereals, chips, popcorn, granola, and almonds. The device can precisely package goods in a range of bag shapes and sizes, guaranteeing their freshness.
- Powdered items: Powdered items including coffee, milk powder, flour, sugar, and spices are often packaged using VFFS equipment. Accurate portion control is ensured by the weighing mechanism.
- Frozen Foods: VFFS is an effective way to package frozen fruits, vegetables, and ready-to-eat frozen meals while preserving product quality.
- Baked Goods: Cookies, crackers, and other baked goods are packed effectively while preserving their quality and hygienic conditions.
2. Pharmaceutical Industry
- Tablets and Capsules: To ensure precision and adherence to industry standards, the pharmaceutical sector packages tablets and capsules in tiny pouches using VFFS equipment.
- Supplements & Powders: VFFS machines provide accurate and impenetrable packaging for vitamins, nutritious powders, and dietary supplements.
3. Cosmetic and Personal Care Industry
- Creams and Lotions: VFFS machines are used to package shampoos, lotions, creams, and other personal care items. The equipment guarantees sanitary, clean, and leak-proof packing.
- Powdered Cosmetics: VFFS machines precisely package face powders, foundation powders, and other cosmetic powders, guaranteeing quality and uniformity.
4. Chemical Industry
- Cleaning goods: Powdered detergents, soap powders, and other cleaning goods may be efficiently packaged using VFFS equipment.
- Agricultural Chemicals: The device is used to efficiently, safely, and securely package insecticides, fertilizers, and other chemical goods.
5. Pet Food Packaging
- Dry Pet Food: VFFS machines are capable of packaging dry pet food, including kibble, in a range of sizes while maintaining nutritional content and freshness.
- Treats & Treats: VFFS machines are also used to package dog treats and other pet goodies in an efficient manner.
6. Consumer goods and retail
- Coffee and Tea: VFFS machines can package coffee beans, ground coffee, and tea leaves in different bag sizes, ensuring precise dosage and freshness.
- Confectionery: VFFS is perfect for the confectionery business since chocolates, sweets, and gum are packed in a sanitary and effective way.
7. Industrial and Bulk Packaging
- Powders: VFFS machines are used to package bulk powders, such wheat, cement, or other industrial commodities, in bigger bags, which makes them appropriate for industrial packaging requirements.
8. Frozen and Fresh Produce
- Fresh Fruits and Vegetables: VFFS provides flexibility in bag sizes and contamination prevention for fresh fruit, such as leafy greens, berries, and root vegetables.
9. Beverage Industry
- Powdered Beverages: VFFS machines are used to package goods including health drinks, quick beverages, and powdered drink mixes in single-serving pouches.
- Liquid drinks: The VFFS machine guarantees reliable filling and sealing of tiny pouches containing non-carbonated liquids, like milk, juices, and drinks.
10. Multi-Product Packaging
- Sample Packs and Multi-Serve Packs: VFFS machines are ideal for packaging snack mixtures, sample packs, and multi-serving bags, among other goods, in a single pouch.
The Vertical Form Fill Seal (VFFS) Machine offers solutions that improve productivity, packing quality, and operational efficiency by addressing a number of significant issues that manufacturers and the packaging sector confront. The issues it resolves are broken out as follows:
1. Inefficiency Issue with Manual Packaging
Problem: Manual packaging is labor-intensive, sluggish, and prone to mistakes including uneven filling, improper sealing, and ineffective labor use.
Solution: The whole bag creation, filling, sealing, and cutting process is automated by the VFFS machine. This improves overall operating efficiency by drastically lowering manual labor, increasing throughput, and guaranteeing constant package quality at faster rates.
2. Variable Packaging Quality Issue
Problem: Manual packaging often leads to uneven fill levels, variable bag sizes, and faulty seals, which may result in poor presentation, product waste, and unhappy customers.
Solution: Accurate fill weights, consistent bag sizes, and tight sealing are just a few of the precise packing operations made possible by the VFFS machine. Packaging that is consistently of high quality improves product appearance, reduces waste, and complies with industry requirements.
3. Limited Adaptability to Various Products
Problem: Conventional packaging methods may not be adaptable enough to manage a large range of items, particularly those with varying dimensions, shapes, or packaging specifications.
Solution: Because VFFS machines are so versatile, they can package a variety of goods, including liquids, powders, dry snacks, granules, and tiny objects. They are appropriate for a variety of sectors, including food, chemicals, medicines, and cosmetics, since they can handle a range of bag sizes and packaging materials.
4. Slow Rates of Packaging
Problem: Particularly in high-demand sectors, slow packing rates may result in production line bottlenecks that reduce total output and operational efficiency.
Solution: VFFS machines are designed for high-speed packaging; depending on the product and bag size, they can package up to 55 bags per minute. In large-scale manufacturing settings, this speed enables companies to satisfy high-volume needs and greatly increase productivity.
5. Problem with Inability to Handle Complex Packaging Needs
Problem: Traditional machinery may not be able to handle some items' particular packaging needs, such as multi-layer bags, tamper-evident seals, or specially shaped pouches.
Solution: Manufacturers can satisfy a variety of packaging needs thanks to VFFS machines' adaptable features, which include date printing, multi-layer packaging, and various seal types (such as tear-notch or ziplock). Because of this, VFFS machines are very adaptable and appropriate for a wide variety of goods.
6. Packaging Waste and Product Contamination Issue
Problem: Inadequate sealing and filling mistakes often result in packaging waste and contamination risk, which is especially important in the food and pharmaceutical sectors.
Solution: To reduce product spills, contamination, and packaging waste, the VFFS machine employs precision filling mechanisms and top-notch sealing technology. This guarantees sanitary, safe, and tamper-proof packaging while also preserving the integrity of the product.
7. Inflexible Production Lines Issue
Problem: When alternating between various goods or bag sizes, traditional packaging systems may need a lot of downtime or reconfiguration, which results in wasted production time.
Solution: VFFS machines are built with fast changeover features that make it simple to modify product kinds, bag sizes, and packaging materials with little downtime. This adaptability maximizes uptime by enabling the manufacturing process to quickly adjust to various packaging requirements.
8. Exorbitant operating expenses
Problem: Inefficient use of packaging materials, high labor costs, and maintenance expenditures may all dramatically raise operating costs in manufacturing plants.
Solution: The VFFS machine improves the utilization of packaging materials, minimizes product waste, and eliminates the need for human labor by automating the whole packaging process. Over time, this lowers total operating expenses and boosts profitability.
9. The Challenge of Upholding Hygiene Standards
Problem: Manual packaging often falls short of the stringent hygienic requirements required for packaging in the food, pharmaceutical, and cosmetic sectors.
Solution: Hygiene is a priority in the design of VFFS machines. Numerous variants include sanitary sealing techniques, easy-to-clean parts, and stainless steel structure, guaranteeing that packaging satisfies strict industrial requirements for safety and hygiene.
10. Limited Packaging Versatility Issue
Problem: Businesses who need to package a variety of things may find that many packaging machines are only appropriate for a certain product type or packaging style.
Solution: Because of its adaptability, the VFFS machine can package a variety of goods, including liquids, powders, and solid foods. It is also appropriate for a number of sectors and applications since it can hold many kinds of packing, including gusseted bags, pillow pouches, and stand-up pouches.
The Vertical Form Fill Seal (VFFS) machine greatly increases production, uniformity, and cost-efficiency by addressing a number of important packaging challenges. The primary issues it resolves are as follows:
- Ineffectiveness of Manual Packaging: By automating every step of the process—bag creation, filling, sealing, and cutting—VFFS machines increase throughput, decrease labor costs, and produce goods more quickly and reliably.
- Issue with Variable Packaging Quality: VFFS machines guarantee tight seals, consistent bag sizes, and accurate filling, enhancing each package's quality and consistency while cutting down on waste.
- Limited Capability to Adjust to Various Products: Because VFFS machines are adaptable, they can package a wide variety of goods, such as liquids, solids, and powders, and they may be made to fit various bag sizes and material kinds.
- Slow Rates of Packaging: VFFS machines are designed for high-speed packing; they can handle up to 55 bags per minute, which greatly increases output and satisfies needs for large quantities.
- Unable to Manage Complicated Packaging Requirements: Because VFFS machines are so adaptable, they may be used for a variety of packaging applications, including date printing, zip-lock closures, and tear-notch apertures.
- Packaging Waste and Product Contamination Issue: By using accurate filling mechanisms and superior sealing technology, VFFS machines guarantee low waste, avoid contamination, and preserve the integrity of the product.
- Production Line Inflexibility: VFFS machines provide rapid changeover capabilities that enable little downtime and quick modifications to various product kinds, bag sizes, and materials.
- Exorbitant operational expenses: By automating the packing process, VFFS machines enhance material usage and minimize manpower, hence lowering total operating costs and boosting profitability.
- Difficulties in Maintaining Hygiene Regulations: Easy-to-clean components and hygienic sealing mechanisms are features of VFFS machines' hygienic design, which guarantees adherence to industrial hygiene requirements.
- Limited package Versatility Issue: VFFS machines are perfect for a wide range of sectors, including food and pharmaceuticals, since they are very versatile and can handle different product kinds and packaging needs.
In conclusion, by tackling problems with cost, flexibility, consistency, and efficiency, the VFFS machine optimizes packing procedures, leading to increased output, better product quality, and cost savings for businesses.