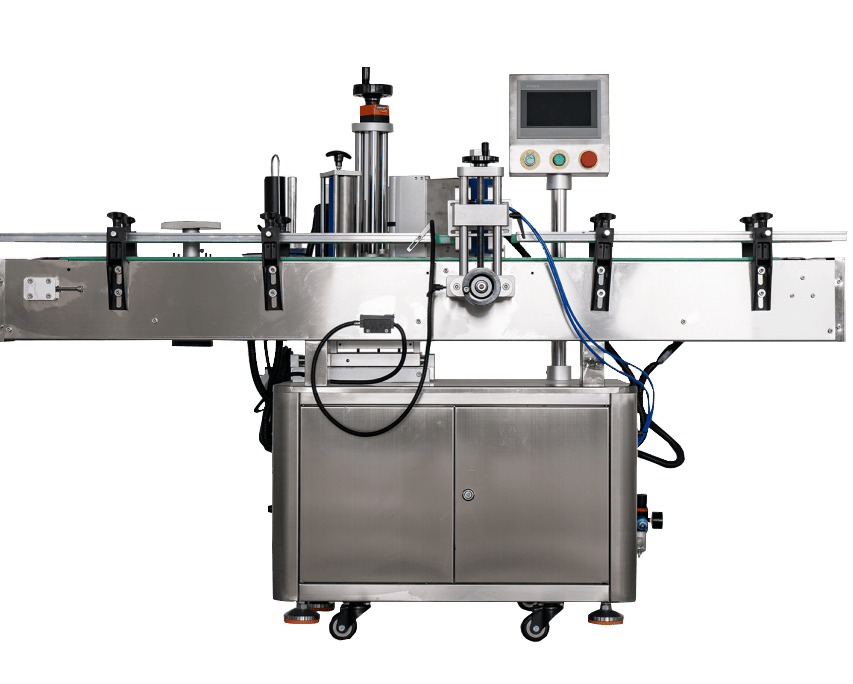
Jar Labeller Machine
Parameter | Specification |
---|---|
Applicable Container Size | Diameter: 25-100mm, Height: 25-300mm |
Label Size | Length: 20-285mm, Width: 20-175mm |
Labeling Speed | 15-45 jars/min |
Labeling Accuracy | ±1mm |
Machine Dimensions | 1900×1000×1450mm (L×W×H) |
Power Supply | 220V/50Hz |
Weight | ~180kg |
MeltVista Jar Labeller Machine can label 15-45 jars per minute for round, flat, or irregularly shaped bottles, ensuring bubble-free and wrinkle-free labeling. Compared to manual labeling, it improves work efficiency by 300% while maintaining a consistent accuracy of ±1mm.
In this era of rapid development, using an automated Jar Labeller Machine is an essential choice for the food, pharmaceutical, cosmetics, and chemical industries. It not only reduces labor costs but also significantly enhances production efficiency.
Labeling machines fall under non-standard equipment in the field of automation machinery. They can be custom-designed based on the shape, size, and characteristics of the products to be labeled, as well as requirements for labeling efficiency, accuracy, and label properties.
Jar Labeller Machine Guide
1. Features and Benefits 2. Applications 3. Overview 4. Working Principle 5. Types of Labeling Machines 6. How to Choose- 300% Faster – Outperforms manual labeling with 15-45 jars/min
- Multi-Shape Compatibility – Handles round, flat & irregular bottles
- Precision Labeling – ±1mm accuracy, smooth application (no wrinkles/bubbles)
- Customizable Design – Modified to fit your exact product specifications
- Easy to Use – Touchscreen interface, quick adjustments, low maintenance
- Heavy-Duty Build – Stainless steel & aluminum construction for durability
Industry Coverage
- Food & Beverage
- Sauces/Condiments: Glass jars (ketchup, honey, jam), plastic bottles (soy sauce, vinegar)
- Alcoholic/Non-alcoholic Drinks: Liquor bottles, beverage bottles, canned goods
- Dairy Products: Yogurt cups, cream containers
- Pharmaceuticals/Healthcare
- Medicine bottles (syrups, pill containers), vaccine vials
- Nutraceutical packaging (softgels, oral liquids)
- Cosmetics/Personal Care
- Cream jars, lotion bottles, perfume bottles, shampoo/body wash containers
- Toothpaste tubes, spray cans
- Chemicals/Industrial
- Lubricant drums, chemical reagent bottles, paint cans
- Electronic component packaging (adhesives, sealants in small bottles)
- Other Industries
- Pet food cans, gardening product bottles (fertilizers, pesticides)
Compatible Container Types
- Shapes: Round bottles, square jars, flat containers, irregular shapes (custom labeling head available)
- Materials: Glass, plastic, metal, ceramic
- Size Range:
- Diameter: 25mm~100mm
- Height: 25mm~300mm (customizable for taller sizes)
The Jar Labeller Machine is a critical automation solution for industries requiring high-speed, precise labeling on jars, bottles, and containers. With rising demand for efficiency, compliance, and branding consistency.
The Jar Labeller Machine market is expanding due to automation demand, regulatory needs, and branding precision. Companies investing in flexible, high-speed labelers gain a competitive edge in food, pharma, and cosmetics.
Need a labeling solution? Share your requirements for a custom recommendation!
Label Peeling Principle
The machine relies on the rigidity and elastic force of the label being greater than the adhesion between the label and its backing paper. By implementing a 172-degree sharp turn on the backing paper, the label is forced to separate from it, achieving the "peeling" process.
Label Feeding Principle
The traction mechanism pulls the backing paper, guiding the label through the peeling mechanism. As the backing paper makes a 172-degree turn at the peeling plate corner, the rigidity of the label surpasses the adhesion between labels, causing the label to detach from the backing paper. As the backing paper continues to be pulled, the label is continuously dispensed, completing the "feeding" action.
Label Application Principle
The label adheres to the target surface with the help of rollers, brushes, or rubber sheets, which apply linear pressure in sequence, ensuring the label is firmly attached to the product surface.
Labeling Machine Control Core Principle
An external signal (usually a product detection signal or foot pedal signal) is input into the control center (typically a PLC). The control center analyzes and processes the input, then sends control signals to drive the motor and traction mechanism, pulling the backing paper and dispensing the label, which is then applied to the target surface.
By Container Shape
1. Flat Surface Labeling Machine
- Suitable Products:
- Cartons and boxes
- Electronics (mobile phone/tablet casings)
- Books and folders
- Food packaging (chocolate boxes, biscuit tins)
- Hardware tool packaging
- Working Principle: Uses vacuum adsorption or roller pressing to accurately apply labels to flat surfaces. Can be integrated with conveyor belts for automatic feeding.
- Technical Features:
- Wide label size range (min 15×15mm, max 300×400mm)
- Labeling accuracy ±0.5mm
- Optional vision system for position verification
- Speed: 60-120 pieces/minute
2. Round Bottle Labeling Machine
- Suitable Products:
- Beverage bottles (water, beer)
- Medicine bottles (oral liquids, injections)
- Cosmetic bottles (serums, perfumes)
- Sauce bottles (ketchup, salad dressing)
- Daily chemical products (shampoo, body wash)
- Working Principle: Rotating mechanism turns bottles while label peeling device applies labels. Available in vertical (bottles upright) or horizontal (bottles sideways) configurations.
- Technical Features:
- Bottle diameter range: φ20-φ150mm
- Speed: 30-200 bottles/minute
- Optional batch number printing
- Hot stamping capability available
3. Irregular Shape Labeling Machine
- Suitable Products:
- Oval bottles (some perfume bottles)
- Square bottles (certain liquor bottles)
- Tapered bottles (essential oil bottles)
- Tubes (toothpaste, ointments)
- Polyhedral containers (some supplement bottles)
- Working Principle: Utilizes multi-axis robots or special fixtures with precision control systems for complex surface labeling.
- Technical Features:
- Customizable labeling paths
- Vision positioning system
- Labeling accuracy ±0.8mm
- Speed: 15-50 pieces/minute
Type | Suitable Shapes | Accuracy | Speed Range | Typical Industries |
---|---|---|---|---|
Flat Surface | Flat surfaces | ±0.5mm | 60-120 pcs/min | Electronics, Food |
Round Bottle | Cylindrical | ±0.3mm | 30-200 pcs/min | Beverage, Cosmetics |
Irregular Shape | Complex curves | ±0.8mm | 15-50 pcs/min | Premium Packaging |
By Automation Level
1. Manual Labeling Machines
- Key Characteristics:
- Operation Method: Requires complete human operation
- Speed: 5-10 pieces per minute (operator dependent)
- Accuracy: ±1-2mm (varies with operator skill)
- Power Requirement: None or minimal (hand-powered models available)
- Ideal Use Cases:
- Prototyping and sample preparation
- Very low volume production (<100 units/day)
- Specialty products requiring careful handling
- Temporary or backup labeling needs
2. Semi-Automatic Labeling Machines
- Key Characteristics:
- Operation Method: Machine applies labels with human assistance
- Speed: 10-30 pieces per minute
- Accuracy: ±0.5-1mm
- Power Requirement: 110V/220V, 50-500W
- Ideal Use Cases:
- Small to medium batch production
- Products requiring precise positioning
- Operations with variable container sizes
- Budget-conscious automation
3. Fully Automatic Labeling Machines
- Key Characteristics:
- Operation Method: Complete automated system
- Speed: 30-400+ pieces per minute
- Accuracy: ±0.1-0.3mm
- Power Requirement: 220V/380V, 1-5kW
- Ideal Use Cases:
- High-volume production lines
- 24/7 continuous operation
- Integration with packaging systems
- Regulated industries (pharmaceutical, food)
Feature | Manual | Semi-Auto | Fully Auto |
---|---|---|---|
Investment Cost | $500-$2,000 | $3,000-$10,000 | $15,000-$100,000+ |
Throughput | 50-100/hr | 500-1,500/hr | 2,000-20,000/hr |
Accuracy | ±1-2mm | ±0.5-1mm | ±0.1-0.3mm |
Labor Requirement | 1 operator | 0.5 operator | 0.1 operator |
ROI Period | Immediate | 6-18 months | 1-3 years |
By Labeling Function
1. Self-Adhesive (Pressure-Sensitive) Labeling Machines
- Core Technology:
- Utilizes pre-coated adhesive labels on silicone-backed release liner
- Employs peel-and-apply mechanism with 165-175° sharp angle peel plate
- Technical Specifications:
- Label Stock: 60-250gsm paper/PP/PET materials
- Application Speed: Up to 1,200 labels/minute (high-speed models)
2. Glue-Based Labeling Machines
- Core Technology:
- Cold glue or hot melt adhesive application systems
- Precision glue pattern control (dot, bead, or spray application)
- Technical Specifications:
- Glue Viscosity Range: 500-50,000 cP
- Temperature Control: 120-180°C for hot melt systems
3. Sleeve Labeling Machines
- Core Technology:
- Heat-shrink or stretch sleeve application
- Steam tunnel or IR heating systems (120-220°C)
- Technical Specifications:
- Sleeve Material: PVC, PETG, OPS films (40-80μm thickness)
- Application Speed: Up to 400 containers/minute
4. RFID/NFC Smart Labeling Machines
- Core Technology:
- High-frequency (13.56MHz) or UHF (860-960MHz) tag encoding
- Near-field coupling antenna systems
- Technical Specifications:
- Tag Placement Accuracy: ±0.5mm
- Data Transfer Rate: Up to 424kbps
By Industry Application
Industry | Specialized Labeling Machine | Typical Applications |
---|---|---|
Food & Beverage | Round bottle labeler, sleeve labeler | Beverage bottles, cans, condiments |
Pharmaceutical | High-precision labeler, RFID labeler | Medicine bottles, syringes, medical packaging |
Cosmetics | Irregular shape labeler, dual-side labeler | Perfume bottles, cream jars, lipstick tubes |
Electronics | Flat surface labeler, QR code labeler | Circuit boards, electronic product packaging |
Chemicals | Corrosion-resistant labeler, drum labeler | Oil drums, chemical containers |
Assess your production demands before choosing a labeling machine. Take into account the daily output volume, the needed speed (manual: 5-10/min, semi-auto: 10-30/min, full-auto: 30-400+/min), and the precision (±0.1mm for high-accuracy sectors like pharmaceuticals, ±1mm for general usage). Next, examine your label type (self-adhesive, glue-based, sleeve, or RFID) and container parameters (flat, round, or irregular forms).
Your production size should determine the amount of automation you need: full-auto for high-speed, integrated lines, semi-auto for medium batches with changeover requirements, and manual for low-volume flexibility. Industry-specific specifications are also important: pharmaceuticals need traceability, food requires hygienic designs, cosmetics require high-end finishing, and industrial applications require long-lasting structure.
Always use real samples for testing, think about future scalability, and balance ROI (usually 6–24 months) with budget. Modular systems that go from semi-auto to full-auto are perfect for expanding companies. For a customized machine suggestion, include your production goals, label specifications, and container samples.