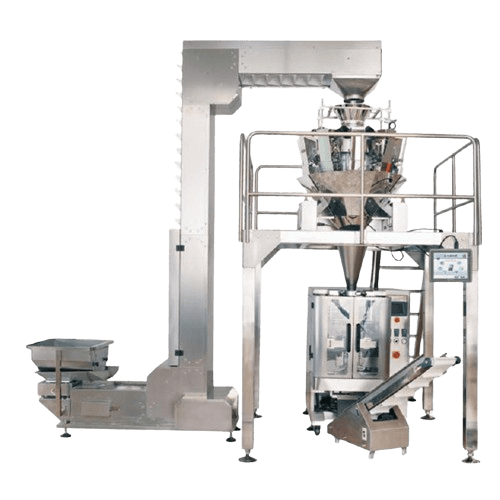
Food Packaging Machine
Column 1 | Column 2 |
---|---|
Row 1, Col 1 | Row 1, Col 2 |
Row 2, Col 1 | Row 2, Col 2 |
Row 3, Col 1 | Row 3, Col 2 |
Row 4, Col 1 | Row 4, Col 2 |
Row 5, Col 1 | Row 5, Col 2 |
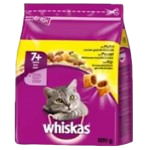
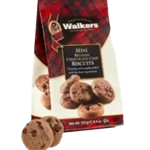
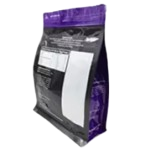
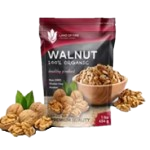
Comprising of four main parts, this Food Packaging Machine is primarily designed for packaging materials in the form of powder, granules, and similar shapes. The machine can package 100-180 bags of material per hour, making it the ideal solution for packaging in the construction, chemical, and food industries.
Characterized by smooth operation, user-friendly operation, and accurate weighing, this Food Packaging Machine can address issues such as pneumatic card opening causing material spillage and bag overturning, which are common in similar products. It outperforms other packaging machines and is often suitable for small to medium-sized factory production.
If you would like to obtain detailed specifications about the MeltVista Packaging Machine, please contact us now for more information!
Food Packaging Machine Guide
Describe Applications of Food Packaging Machines How to Choose the Right Food Packaging Machine Types of Packaging Machines Offered by Meltvista ConclusionProduct Description:
- The Food Packaging Machine is a multipurpose tool made especially for packing food particles and powders. This equipment guarantees accurate and dependable packaging for a range of food goods by utilizing cutting-edge technology and effective procedures.
- The Food Packaging Machine can handle both food granules and powders thanks to its high-standard production procedure. Its production procedure makes use of stainless steel and carbon steel to guarantee both longevity and adherence to food safety laws. The food items' integrity is preserved by the efficient and consistent packing made possible by the dual-screw feeding system.
Benefits:
- Increase productivity and efficiency through automation.
- Reduce costs through optimal material use.
- Support branding and marketing.
- Preserve freshness by removing air.
- Extend shelf life with controlled environments.
- Enable customized packaging.
- Comply with regulations.
- Provide traceability and quality control.
- Handle a variety of products.
- Minimize environmental impact.
- Help save money and yield a positive return on investment.
Chemical Industry:
- Precision and Safety: Chemicals must be packaged in extremely exact amounts to guarantee both safety and legal compliance. By offering precise dosage control, automatic packaging devices lower the possibility of human mistake.
- Chemical Defense: Chemicals may be bad for people's health and the environment. By reducing manual interaction, automatic packing devices reduce the risk of hazardous material exposure for the operator.
- Preventing Pollution: By limiting product-to-environment interaction, automatic packaging solutions assist ensure the purity and quality of chemicals while also lowering the danger of contamination.
- Enhanced Effectiveness: Chemical manufacturing requires large-scale production, and automatic packaging equipment greatly increase packing speed and total production efficiency.
- Observance of Regulations: Strict rules and restrictions apply to the chemical sector. Labels, packing materials, and product amounts may all be precisely created and altered in automatic packaging equipment to guarantee compliance with these laws.
- Variety in Packaging: Chemicals can be liquids, powders, or granules, among other forms. Automatic packaging machines can handle many kinds of chemicals because of its multifunctionality.
- Control of Quality and Traceability: Chemical packaging machines, like their food sector counterparts, may be equipped with traceability and quality control systems to facilitate batch monitoring and guarantee that quality requirements are met.
- Sustainability of the Environment: Certain chemical packaging machines encourage the use of environmentally friendly materials, which cut down on packaging waste and promote sustainable development principles.
Milk Powder Industry:
- Accurate Dosage Management: Food packaging machines can ensure that milk powder is packaged in accordance with exact formulae and standards, minimizing the chance of human mistake. They can also provide very accurate dosage management.
- Variety in Packaging: There are several types of milk powder, including whole milk powder and skim milk powder. Food packaging machines can handle a wide range of milk powder packaging kinds and requirements because of their adaptability.
- Effective Packaging Method: Milk powder packaging speed may be increased using automated food packaging equipment, improving total production efficiency and guaranteeing high output while upholding quality and hygienic requirements.
- Assurance of Hygiene Standards: Food packaging machines are made of materials that are simple to clean and sterilize, guaranteeing that milk powder satisfies hygienic requirements and is not contaminated throughout the packaging process.
- Tailored Packaging: Food packaging machines may produce customized milk powder packaging, including labels, packing forms, and overall design, based on brand specifications and market expectations.
- Increased Product Life: By limiting the amount of time milk powder comes into contact with outside air, automation systems that regulate packaging conditions assist increase product shelf life and decrease waste.
- Eco-Friendly Packaging: In keeping with sustainable packaging standards, certain food packaging machines encourage the use of environmentally friendly materials, which helps to lessen the environmental effect of milk powder packing.
- Observance of Regulations: Milk powder packaging meets with food safety and quality standards because food packaging equipment may be set to satisfy regulatory criteria.
Coffee Industry:
- Food packaging machines are essential to the coffee business because they offer accurate, sanitary, and efficient packaging options. With the use of technologies like vacuum or modified environment packaging, these machines extend the freshness of coffee and assure precise coffee mixing. They can also handle other kinds of coffee packing, such as beans, powder, or capsules. They also address the demand for easy single-cup solutions, facilitate customized and ecological packaging, and improve overall manufacturing efficiency. While the design of the machines assures compliance with cleanliness standards and food safety regulations, the use of eco-friendly materials is in line with the industry's rising focus on sustainability. In the end, coffee industry food packaging devices satisfy customer demands for inventive, premium, and eco-friendly coffee experiences.
Key Considerations:
- Raw Materials: Consider the physical form, sensitivity, shelf life conditions, size and type of packaging container, viscosity and flowability, leak prevention requirements, and look conditions for packaging.
- Production Volume: Determine the required units per minute or per hour of packaging, align with the preferred packaging form, choose the right level of automation, and prioritize machine durability, convenience of use, and maintenance.
- After-Sales Support: Opt for a supplier that provides comprehensive training, technical assistance, spare parts availability, online support, remote monitoring, warranty policies, service contracts, and maintenance agreements.
Semi-Automatic Powder Packaging Machine:
- This series of packaging machines utilizes a combination of screw filling and electronic weighing feedback for measurement. Microcomputer control provides automatic quantification, filling, error correction, counting, and material clearing. It can package 20 bags per minute with a weight range of 1-10 kg and occupies a small footprint.
- It is suitable for quantitative packaging and filling of powder and granular mixed materials in industries such as pharmaceuticals, chemicals, food, and agricultural products. Applications include composite seasonings, natural flavorings, food additives, fragrances, flour, milk powder, protein powder, solid beverages, sugar, monosodium glutamate, pesticides, veterinary drugs, laundry detergent, enzyme preparations, feed additives, chemicals, and new building materials.
Powder Quantitative Packaging Machine:
- Characterized by smooth operation, user-friendly operation, and accurate weighing, this powder quantitative packaging machine is designed for the precise packaging of powder materials. The HZ-A25 model powder quantitative packaging machine consists of four main parts: an automatic weighing device, conveying device, sewing device, and computer control. It features a rational structure and an aesthetically pleasing design, with the main unit employing fast, medium, and slow feeding speeds and a dual-feed screw structure. The machine utilizes PLC frequency control technology, sampling processing technology, and achieves automatic error compensation and correction, making it suitable for the quantitative packaging of powdered materials.
- With a packaging speed of 120-180 bags per hour and a packaging weight range of 10-50 kilograms, the overall construction incorporates carbon steel and stainless steel processes. The machine is easy to operate, enhancing operational efficiency.
Granule Quantitative Packaging Machine:
- This machine is primarily composed of four main parts: an automatic weighing device, conveying device, sewing device, and computer control. It features a rational structure, aesthetically pleasing design, stable operation, user-friendly operation, and accurate weighing. It is suitable for the quantitative packaging of granular materials.
- The main unit operates at fast, medium, and slow feeding speeds, with PLC LCD display, sampling processing technology, and automatic error compensation and correction. The packaging specifications range from 10-50 kilograms, and the packaging speed is 180-240 bags per hour.
Powder Premade Bag Automatic Packaging Machine:
- The packaging machine implements self-automatic detection and information feedback functions. During production, if there is no packaging or the packaging bag is not open, the detection device controls no filling and no sealing, and the real-time display of the operating status results in automatic shutdown. This saves packaging materials and raw materials, ensuring a clean packaging environment and preventing raw material contamination.
- Screw Metering Device: The powder screw filling device is an independent metering filling system. This device utilizes a high-precision stepper motor to drive the screw for filling. Within the machine's metering range, different-sized screws can achieve varying metering ranges. It is easy to operate, convenient, and precise.
- Screw Feeder: The filling motor-driven screw has advantages such as accurate positioning, high precision, fast speed, large torque, long life, adjustable speed, and good stability. By changing screw accessories, it can adapt to various materials from ultra-fine powder to large particles.
- Variable Frequency Speed Control: This machine employs variable frequency speed control, allowing the packaging weight to be adjusted continuously. The operating status can be changed at any time, providing convenient operation.
- Quick Change of Packaging Bag Specifications: The mechanical arm device facilitates easy and fast debugging, overcoming the disadvantage of weight changes due to variations in material density.
- The packaging machine can produce various bag types, such as stand-up bags, flat bags, handle bags, zipper bags, four-side sealed bags, three-side sealed bags, paper bags, M-shaped bags, etc., made from composite film.
- Horizontal Bag Delivery: The bag storage can accommodate more packaging bags, with lower requirements for the quality of the formed bags, resulting in high bagging and sealing rates.
- No Dust Leakage: The filling outlet is equipped with a dust suction device, protecting the workshop environment.
- Finished Product Conveyance: Stable operation, high resistance to interference, high weighing accuracy, convenient operation, and intuitive operation.
Combination Weighing Fully Automatic Packaging Production Line:
- This production line is capable of packaging various solid materials, liquids, sauces, powders, and granules, including candies, peanuts, coffee beans, goji berries, pistachios, rock sugar, seeds, nut preserves, frozen foods, curry powder, chili powder, salt, monosodium glutamate, chicken essence, milk powder, chemical seasonings, fine white sugar, pesticides, veterinary medicine powder, laundry detergent, etc. Its notable features include replacing manual packaging with machinery, achieving automation in enterprise product packaging production, with packaging weights ranging from 50-1000g and dimensions of width 80-220mm and length 130-380mm. It can package 10-50 bags per minute.
- The production line significantly enhances enterprise production efficiency, drastically reduces product costs, and effectively minimizes material pollution in the packaging process. It boasts high-quality and aesthetically pleasing packaging, making it suitable for large-scale automated packaging of food products. The bagging machine replaces traditional manual labor, realizing automation in enterprise product packaging production, thereby improving efficiency and reducing costs. The equipment employs materials processing that complies with food hygiene requirements, ensuring the hygiene and safety of food products.
- The machine's packaging capabilities are extensive, accommodating various solid materials, liquids, sauces, powders, and granules. It is adaptable to a wide range of packaging bags, including those made from multi-layer composite films, single-layer PE, PP, and other pre-made bags or paper bags. The electrical control system utilizes advanced PLC technology with a color POD (touch screen), ensuring user-friendly operation. The main motor incorporates variable frequency speed control, allowing the frequency to be freely set within a specified range.
- Food packaging machines play a pivotal role in various industries, offering a multitude of benefits ranging from increased productivity and efficiency to compliance with regulations and sustainability practices. Whether in the chemical, milk powder, or coffee industry, these machines provide precise dosage control, safety, and environmental protection.
- When choosing the right food packaging machine, considerations such as raw material characteristics, production volume, and after-sales support are crucial. Machines need to align with the physical form and sensitivity of raw materials, packaging container requirements, and production scale. Robust after-sales support ensures long-term performance and efficiency.
- Meltvista offers a diverse range of packaging machines, from semi-automatic powder packaging machines to fully automatic production lines, each tailored to specific industry needs. The incorporation of advanced technologies, such as vacuum packaging and modified atmosphere packaging, ensures freshness and shelf life extension.
- Ultimately, selecting the right food packaging machine requires a careful evaluation of raw material properties, production requirements, and scalability. By prioritizing efficiency, ease of use, and maintenance, businesses can make informed choices to optimize their food packaging operations and achieve long-term success.